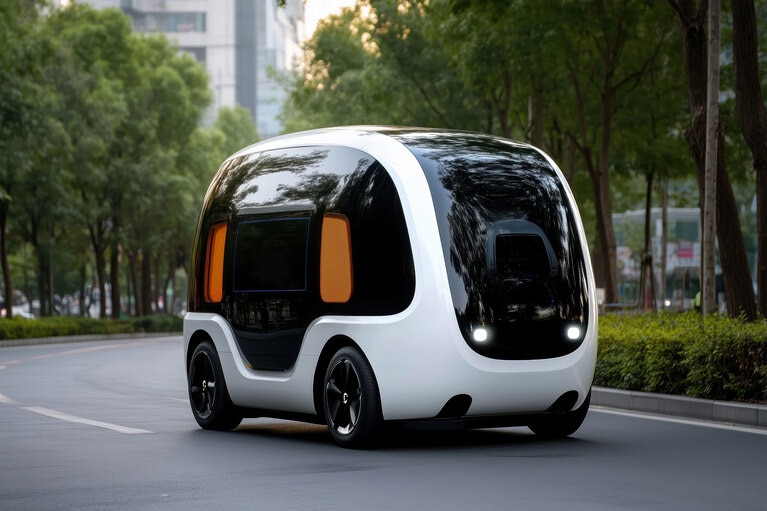
自動運転EVシャトルの給電能力と信頼性と安全性を最高レベルで実現する、電源モジュールの優れたパッケージング
自動運転EVシャトルの給電能力と信頼性と安全性を最高レベルで実現する、電源モジュールの優れたパッケージング
A voltage regulator provides two functions: changing the input voltage to a different level at the output and regulation (maintaining a constant output voltage despite changing load conditions). DC-DC regulators are a key component in any power system, and so choosing the correct regulator is critical if an optimum solution is to be developed.
Although engineers understand regulator functionality, less experienced engineers often find it difficult to identify the best regulator for their application. This blog post identifies criteria that anyone who is not an experienced power developer can use to ensure they choose the perfect regulator.
There are three basic categories:
In most applications voltages are stepped down from the bus to the load and therefore buck regulators are commonly used. Other applications require the voltage to be increased with a boost regulator: for example, if DC power must be transmitted using a long cable, the I2R losses can be reduced by boosting the voltage before transmission and then stepping it down again at the load. In battery applications buck-boost regulators are often used to provide a constant stable voltage, overcoming the change of output voltage that is seen as batteries charge and discharge.
Many systems have clear requirements for input and output voltage – for example, you may need to step down a 12V rail to 3.3V. For many applications, there will be a suitable regulator available off-the-shelf to meet the voltage requirements.
Obviously, the regulator must be able to deliver the power required by the load. Regulator power is typically specified by a maximum output current.
Although applications often require a specific voltage, others will require an adjustable output. This might be because the loads change – for example in a piece of test equipment – or it may be that the load is supplied by a long cable, and the voltage needs to be trimmed a little higher than required by the load to compensate for the voltage drop across the cable.
Input voltage ranges are particularly important for applications such as battery-powered systems. In an automotive application, a nominal 12V battery might deliver 12.5V at full charge and drop to 10V or less as the battery discharges. A regulator with a narrow input range may no longer function as the battery voltage drops, meaning that the full capacity of the battery cannot be used. Ensuring a sufficiently wide input range is therefore an important criterion for selecting your regulator.
Choosing wide input regulators also has another benefit: they can also reduce inventory costs as a single regulator can be used in a variety of different situations.
Efficiency is one of the criteria for most power systems designed today. Selecting a regulator with high power losses can make it almost impossible to meet efficiency goals. It’s important to also remember that regulator efficiency is not constant: typically, the efficiency of the regulator will fall dramatically as the step-down or step-up ratio increases and as the current drawn from the output decreases.
Modern regulators, such as those based on Vicor’s Zero Voltage Switching (ZVS) topology offer inherently high efficiency and are more consistent across the whole operating range.
Switching regulators provide high efficiency, but the switching circuit generates noise. In some systems, particularly those with sensitive analog components, the power supply noise can limit overall performance. Unnecessary electronic noise can also make it more difficult to achieve EMC certification.
As with efficiency, the regulator topology is key to achieving low noise: it’s much easier to use a component that doesn’t generate noise than it is to try to filter that noise out. ZVS, for example, is a soft-switching topology that is inherently low-noise, making it easier to develop high-performance systems.
Today electronic systems are often space constrained. Even if the goal is not to make the system as small as possible, such as products housed in standardized 19” rack units, reducing the size of the power system allows the space saved to be used to add additional functionality.
Any calculation of size should also consider the peripheral components required by the regulator. With higher levels of integration and high switching frequency, the size and number of peripheral components can be reduced, which can potentially offer a greater space-saving than simply picking a regulator in a smaller package.
The package types available don’t only determine the space required: often smaller packages can be located closer to the load, enabling more accurate regulation at the load and faster transient response.
In addition to size, weight can also be an important factor, particularly in applications where the equipment can move. Examples of such systems range from hand-carried portable equipment to automotive electronics and drones.
Regulators cannot be 100% efficient, so they will always dissipate heat that must be removed. If a heatsink is required, this can significantly increase both the size and weight of the power system. Failure to dissipate heat can also impact the system performance in other ways: for example, in lighting or display applications if the regulator causes an increase in temperature of the LEDs, this will reduce the intensity and change the wavelength, and therefore the hue, of the light generated.
The regulator must function reliably across the range of temperatures to which it can be exposed. In general, more efficient regulators will be able to operate at higher temperatures, as they do not need to dissipate so much heat, but products from different suppliers can vary widely so it is important to check the data sheet.
In addition to the criteria described above, your application may require some specific functionality, which can limit choice. Examples of these additional features include:
Although regulators are conceptually simple components – they take a voltage at the input and deliver a different voltage at the output – there are many factors that determine the best regulator for your application. Carefully considering the criteria outlined above will help to ensure you pick the ideal regulator for your system.
Product overview: ZVS regulator evaluation board
Product overview: ZVS buck regulator
Product overview: ZVS buck-boost regulator
自動運転EVシャトルの給電能力と信頼性と安全性を最高レベルで実現する、電源モジュールの優れたパッケージング
自動運転EVシャトルの給電能力と信頼性と安全性を最高レベルで実現する、電源モジュールの優れたパッケージング
High-bandwidth power modules quell the disruption of high-voltage line ripple rejection
Vicor DC-DC converters combine high bandwidths with soft switching topologies to reduce EV ripple rejection more effectively than conventional solutions
ディスクリートの電源ではなく電源モジュールが選ばれる理由とは
信頼性、スケーラビリティ、サイズと重量、電源設計に求められる専門知識などの要素を分析することで、2つの設計手法の違いを明確にし、モジュールで構成する電源システム設計の利点を抽出します。
High-density power modules boost performance for a new generation of mobile robots
Minimizing size and weight are important in robotics design, but increasing power is essential for supporting new sensors, peripherals and features.