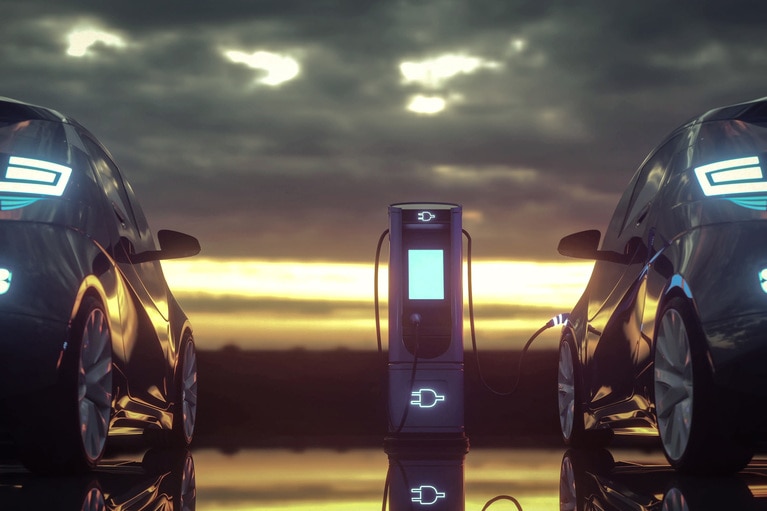
High-bandwidth power modules quell the disruption of high-voltage line ripple rejection
Vicor DC-DC converters combine high bandwidths with soft switching topologies to reduce EV ripple rejection more effectively than conventional solutions
EMI is seen as one of the key challenges of power conversion design and system integration, particularly for AC-DC systems. Our latest technical tip by David Fletcher, Principal Engineer from Vicor’s Westcor Division, looks at the causes of EMI and its impact on a system, before going on to make some practical suggestions on how to minimize its effect.
We have to start with what engineers affectionately call noise. This is generated whenever rapid voltage (dv/dt) and/or current (di/dt) transitions take place. AC-DC power converters typically utilize a number of power switching topologies, including fully resonant, quasi-resonant and PWM (Pulse Width Modulation), the most typical control in the front-end section of the converter.
PWM-controlled converters use a rectangular control signal with a continuously varying pulse width in response to the operating conditions of the converter. The result is typically a “white noise” energy distribution spectrum. If this was not filtered and shielded it would interfere with consumer electronic equipment using the same AC mains.
“Noise” currents exiting the power converter through the AC power lines and/or via output power cables are known as “conducted emissions.” The noise manifests itself in two forms: differential and common-mode. The definition of differential-mode is noise that is only on the power lines and is not present on the earth ground lead, and can be measured with respect to the power lines. The definition of common-mode is noise that can only be measured from earth ground to one of the power lines.
AC-DC power converters employ EMI filters within the power converter enclosure. These filters contain noise suppression topologies containing inductive and capacitive components. These components are called “X” and “Y” elements. The “X” components are placed across the power lines and filter the differential-mode noise; the “Y” components are placed between the power lines and earth ground and filter common-mode noise.
AC-DC power converters are designed to meet various regulatory and safety standards, including various EMI standards. The individual details and the standards met are generally covered thoroughly in the product literature. However, during a system integration of various components, including an AC-DC power converter, a system design engineer may find it necessary to add additional EMI filtering to enable the integrated system to comply with all relevant agency standards. If this approach becomes necessary, it is recommended to minimize the additional filter components required by empirically gathering test information. It is recommended that a few areas be given special attention:
If EMI problems still persist, then adding an external filter may be necessary. There are areas to consider when considering an off-the-shelf filter:
High-bandwidth power modules quell the disruption of high-voltage line ripple rejection
Vicor DC-DC converters combine high bandwidths with soft switching topologies to reduce EV ripple rejection more effectively than conventional solutions
The future of standardized defense platforms using MOSA, SOSA and VPX open architectures
Using open standards to increase interoperability, scalability, reliability, reduce system costs, and minimize the number of custom electronics designs
Delivering higher power density and low noise for New Space applications
Patented power design techniques and architectures needed to deliver optimal power and low noise for space communications applications
Optimizing high-density power design: modular vs. discrete
There are several important design variables to consider when evaluating the power module design process