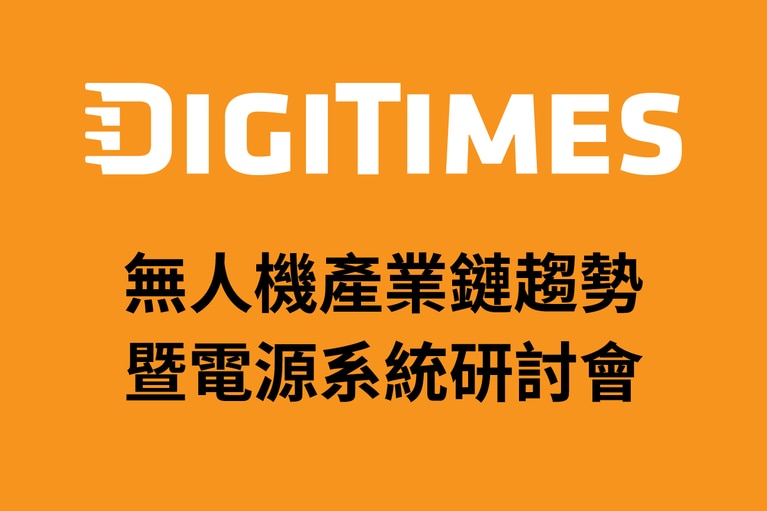
2025 台北無人機產業鏈趨勢暨電源系統研討會,台灣
Power levels are rising across many industries, and many users are now considering moving their PDN away from 12V to try to ease those challenges.
By Henryk Dabrowski, Vicor VP of Sales for EMEA
Figure 1: Vicor highest systems performance power modules.
Every electronic piece of equipment or system has a power delivery network (PDN) made up of cables, bus bars, connectors, circuit board copper power planes and AC to DC and DC to DC converters and regulators. Governing the performance of a PDN is its overall architecture, such as the use of AC or DC voltage distribution, specific voltage and current levels and when and how many times the network needs voltage conversion and regulation.
Many PDNs have been standardized in specific industries over many years, such as 270V and 28V in the Defense and Aerospace industry, the negative 48V used in communications infrastructure applications and the 12V PDN used in automobiles which then became a standard in computer servers and industrial applications. As a result, billion dollar industries were built around standard PDNs.
As industries transition to new PDNs such as 48V, 400V and 800V, there are many opportunities to substantially improve performance with non-traditional power delivery architectures and technologies.
Advanced systems in enterprise and high-performance computing, communications and network infrastructure, autonomous vehicles and numerous transportation applications are just a few of the high-growth industries clamoring for more power. These systems with their ever-increasing number of loads, and load power, pose complex design challenges for achieving high performance when the PDN is based on 12 volts. Incorporating higher voltages has challenges and there are good reasons to resist change due to the long successful history and use of 12V and the massive supply chain ecosystem that has been built over decades.
Figure 2a: Vicor PDN 3-Phase 12V.
Figure 2b: Vicor PDN 24V.
The telecommunications industry has been using a 48V PDN for decades. 48V was the best option because:
As communications networking infrastructure grew in complexity with the advent of the internet, laptops and mobile phones, the 48V PDN infrastructure had to power the many new and complex loads consisting of arrays of network processors, memory and control system loads. This posed a challenge because the bulk of the available technologies were centered on 12V capabilities with semiconductor converters and regulator components optimized for this operating voltage.
To solve this 48V to 12V problem, an architecture called IBA (Intermediate Bus Architecture) was deployed and quickly became the de-facto standard in communications and network infrastructure applications. Intermediate bus converters (IBC’s) which are isolated, non- regulated fixed ratio (1/4) converters were developed by several companies and built on an open frame package that met DOSA and POLA pin out standards to enable multi-sourcing.
Advanced systems in enterprise and high-performance computing, communications and network infrastructure, autonomous vehicles and numerous transportation applications are just a few of the high-growth industries clamoring for more power. These systems with their ever-increasing number of loads, and load power, pose complex design challenges for achieving high performance when the PDN is based on 12 volts. Incorporating higher voltages has challenges and there are good reasons to resist change due to the long successful history and use of 12V and the massive supply chain ecosystem that has been built over decades.
Figure 3: Vicor PDN minus 48V.
Isolation was not a safety requirement for the SELV IBA because positive battery terminals were tied to ground to stop galvanic corrosion, resulting in a negative 48V voltage. By using an isolated fixed-ratio bus converter as a DC-DC transformer, a –48V input could then be used to deliver a +12V output for the downstream point-of-load (PoL) regulators. By using an isolated fixed ratio bus converter as a DC to DC transformer, a –48V input can be used to deliver a +12V output for the downstream point of load (PoL) regulators.
Advanced applications such as artificial intelligence (AI) in data centers are driving the move from 12V to 48V PDNs and away from IBA to new architectures. The significant rise in processor and associated server rack power levels has simply exceeded what 12V and IBA can deliver.
For the automotive market, the need to meet legislation and new standards that required a reduction of CO2 emissions in vehicles was a catalyst to explore vehicle electrification. This has resulted in the emergence of 48V batteries to support new mild-hybrid powertrain, safety and entertainment system designs.
With the advent of higher system power requirements, PDNs based on 380V and 48V are more complex as many industries are still trying to retain legacy 12V PDN infrastructure at the point of load. Additional PDN challenges come in the form of new high-voltage bulk power sources such as 800V batteries in pure electric (EV) and high-performance vehicles.
In these new systems and applications power delivery can be broken down into three basic segments:
The opportunities for innovating bulk power conversion to an intermediate 48V PDN, lie in the following areas:
As power levels continue to rise, the challenges on a bulk power system design get increasingly more complex. Managing the size and weight of the bulk power converter and cooling it due to higher power losses are the primary areas of focus in the majority of applications. If size and weight is not an issue then very high efficiency can be achieved and thermal management can be achieved with fan cooling.
Figure 4: HV to 48V.
However, most applications are demanding higher power density. Power systems engineers should consider the benefits of using power modules for designing and building these large converters, rather than ground up discrete based designs. Power modules in conjunction with innovative architectures, topologies, control systems and packaging, offer new ways of improving bulk PDN performance.
If the bulk power source is AC or high voltage DC then isolation is required. An isolation stage adds power loss in any converter, but regulation may not be necessary if the intermediate bus PDN contains regulation for the PoL stage (i.e. 48V to 12V). The two considerations for this approach are
Figure 5: 48V to 12V isolation.
Data centers and exascale computing commonly require maximum processing power in a confined space, so they benefit greatly from high density component and advanced cooling techniques. In some cases, full immersion cooling is being implemented where the entire server is placed in a bath of Fluorinert. Alternatively, other high performance computing applications are developing cooling techniques with heat pipe and cold plate technologies. In these applications a low-profile planar package is required for the power conversion and regulation stages of the bulk power system.
Figure 6: DC-DC conversion and regulation.
Innovating Intermediate bus and Point-of-Load power delivery
The opportunities for innovating 48V intermediate bus PDNs lie in the following areas:
Moving from a 12V intermediate bus PDN to a 48V PDN presents challenges but also offers advantages. Maximizing the 48V power delivery as close as physically possible to the PoL regulators will reduce cable, connector and PCB copper power plane, size, weight and cost. PoL space constraints are often problematic, so the converter needs to have a high power density and efficiency. A non-isolated fixed-ratio bus converter is the best option as long as the PoL regulators can handle the voltage variation on their input which is determined by the voltage input range to the bus converter divided by the turns ratio or K factor (VIN / K = VOUT). If the bulk power converter is designed with reasonable regulation tolerances, then this design approach is both feasible and advantageous.
For designs where the bulk power converter or bulk power source (such as a 48V battery) has a wide output voltage range, then regulated DC–DC converters may be required depending on the PoL regulator input voltage specification. Adding regulation to the 48V to 12V stage reduces the efficiency of the converter by 2% to 4% depending on its topology.
To really advance the PDN design, with significantly improved performance and high current density at the PoL, a new architecture to consider is the Vicor Factorized Power Architecture or FPA. With FPA a new type of converter called a current multiplier, which is capable of direct 48V-to-load voltage conversion with high efficiency and density, is placed very close to the load. In high-current applications this is very advantageous as it reduces the PDN impedance between the converter to the load which can be a source of very high power losses and also impact di/dt transient performance.
Because the current multiplier is a fixed-ratio converter, an upstream regulation stage is needed to complete the FPA design. To maximize efficiency and density while minimizing power losses, the regulator module operates with both input and output voltages set to 48V, with the current multiplier K factor chosen to provide the required output voltage for the load.
As power levels rise across many industries, moving to a higher voltage PDN can ease the challenge but also add complexity. Power systems engineers should evaluate new topologies and architectures from new suppliers that can deliver appreciable system performance benefits. Progress, advancement and innovation invariably require new thinking, new ideas and new approaches. As your business requirements change, be open to possibilities. Exploring and researching alternatives can be rewarding in many ways.
This article was originally published by Power Systems Design.
Henryk Dabrowski has over 25 years experience in technology design, commerce and leadership. As Vice President of Sales for EMEA, Henryk is responsible for working with customers to introduce the most robust, effective and innovative technological solutions.
Prior to joining Vicor in 2013, Henryk held commercial roles at semiconductor businesses Texas Instruments and Infineon, and roles at European components distributor Rutronik. In July 2005, Henryk achieved Chartered Engineer status with the Institute of Engineering and Technology (IET) and the Engineering Council UK and has continued his professional development by following The Leadership Programme at Henley Business School.
Henryk Dabrowski, Vicor VP of Sales for EMEA