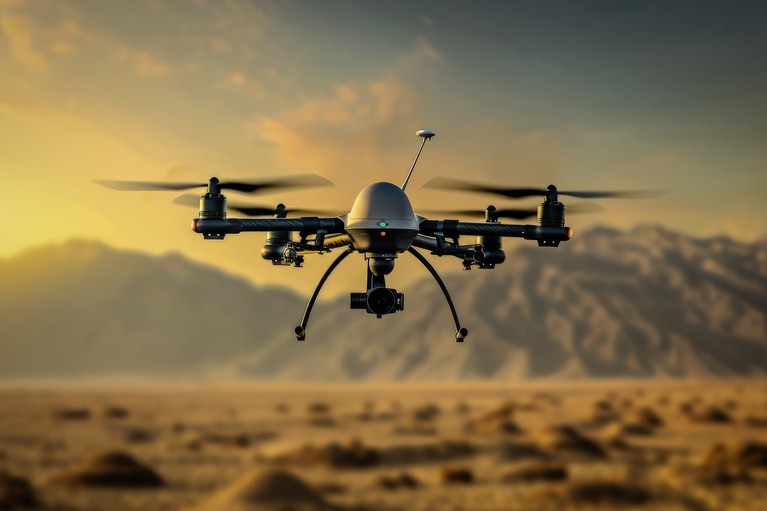
Build better UAVs using modular power
Power Delivery Networks (PDN) based on Vicor high performance power modules enable innovative designs for the next generation of UAV development
Recent improvements in sensors and software allow autonomous robots to identify and avoid human workers or other obstacles and to travel to their destination by the shortest route, rather than being limited to defined robot pathways. These nimble robots are required to carry parts or finished goods 24/7 as a key contributor to the SMART factory, providing faster delivery and lower costs. This manufacturer of robots was looking to maximize time between recharges without impacting other performance factors. The key goals were:
The power for the robot came from a 48V battery stack, which powered the motor drive directly. The power supply was required to convert the battery input to three rails of 6V and one of 12V to power the sensors, navigation interfaces and CPU. The solution was based on four arrays of Vicor PRM and VTM converters, one array for each output. Key benefits were:
Small footprint, low profile (6.7mm)
Lowest losses achieved by high efficiency conversion (>92.7%)
Lightweight
Four PRM/VTM converter combinations provided the isolation and regulation for each output. The ability to parallel converters accommodated the output powers required (6V at 60W and 12V at 600W). Output rail power sequencing was easily achieved though configuration of the PRMs. To analyze this power chain go to the Vicor Whiteboard online tool.
Build better UAVs using modular power
Power Delivery Networks (PDN) based on Vicor high performance power modules enable innovative designs for the next generation of UAV development
UAV Market Trends and Power System Seminar 2025 Taipei, Taiwan
Power modules enable top performance and innovation for today’s advanced UAVs
High-efficiency, high-density modules free up space for advanced communications and extend range
High-efficiency class of UAV depend on solar power to meet its long flight time requirements
High-density, high-power modules enable lighter, safer, lower cost tether cables to extend missions
This class of unmanned vehicle is powered and controlled via a tether from a ground-based power source assisting in extended missions