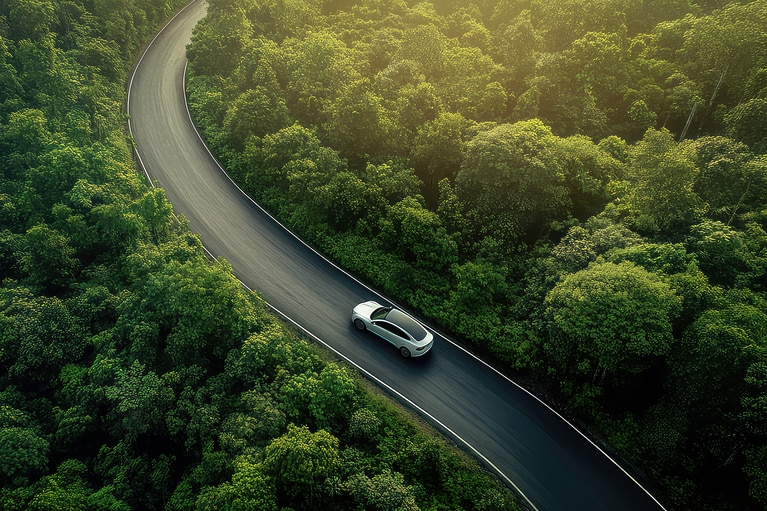
汽车主动悬挂系统
48V 电源系统可减少损耗并缩小电源设计。Vicor 使 12V 至 48V 的过渡变得更容易,获得 竞争优势
随着原始设备制造商(OEM)采用 48V 电源架构,他们正努力优化其电源系统设计。Vicor 的高功率密度模块体积小、重量轻,是高压转换的理想选择,可以为 48V 区域架构提供峰值效率。
作者:Greg Green,汽车客户项目总监
阅读本文,您将了解:
汽车的发展一直处于颠覆性变化和增长的状态,且没有放缓的迹象。从汽车如何移动,到如何与乘客及其他车辆互动,每一个方面都在发生变化。这一点不仅适用于汽车本身,还适用于周围的社会基础设施,从电动汽车充电系统到智慧城市的互动。
在汽车电气化方面,切换动力来源并用电机驱动车辆是简单直接的方面。但要开发下一代电动汽车,必须全面考虑整车的设计。
例如,在依靠内燃机驱动车辆的传统燃油车中,通常有一个交流发电机或发电机组,发电量通常超出汽车所需的平均水平。这些系统通常根据具体设计提供低至 12V 或 24V 的电源。
因此,汽车电源设计工程师的工作相对简单,他们大致知道汽车需要多少电力,并且知道这不会限制车辆的行驶距离或速度。然而,对于现在的电动汽车,情况突然发生了变化,开灯或听收音机会影响到续航里程。这就迫使汽车设计师进行权衡,因为电池中的电力既要用于驱动车辆,也会用于其他用途,这样会缩短续航里程。
现代电动汽车的一个重要方面是它们使用更高的电压,通常为 400V 或 800V。高压是一种安全隐患,因此车辆设计师必须考虑高压区域与接触点或司乘人员所在位置的关系。
大多数电动汽车的车内工作电压为 12V。尽管多年来 48V 一直是汽车界的目标,但这需要设计全新的发电机,以及 48V 泵、压缩机、雨刷电机等,因此其发展一再被延误,直到最近才有所改观。
现在,汽车行业可以开始在车辆配电网络中利用 48V 的优势。然而,汽车设计的核心最终仍然归结为汽车行业的两个关键词:成本和重量(见图 1)。48V 系统的优势在于主电缆更小,铜用量更少,意味着它们重量更轻,成本更低。另一个优势是这些电缆的线径要小得多,因此车内的物理布线更加容易。
图 1:成本和重量是汽车原始设备制造商考虑的主要因素。48V 系统的优势在于主电缆更小,铜用量更少,这意味着汽车重量更轻,成本更低。另一个优势是这些电缆的线径要小得多,因此车内的物理布线要容易得多。
采用 48V 电源架构,再加上区域电源架构的出色能力,我们就可以使用三或四个区域控制器最大限度地减少控制系统和通信电缆,而不是将数十个芯片分散安装在整个车辆中。这样还可以帮助设计师将最大的负载先转换为 48V,从而降低开发和验证新的 48V 雨刷电机或前端照明系统的成本。
在配电网络中实施区域架构,就可以灵活地将部分负载转换到 48V,同时在汽车的前后端及信息娱乐系统中仍使用 12V 电源。在这种混合配电系统中,核心电源为 48V,只是在需要时在局部转换为 12V。这就像嵌入式系统中使用的最新板级配电架构。
面对将高压(HV)(800V 或 400V)转换为 48V,再转换为 12V 的挑战,有几种解决方法。传统方法使用大量分立元件,占用的空间非常大。现在,一种新方法是利用高功率计算系统中采用的微型化技术,并将其改造用于汽车,以满足汽车的所有电压转换需求。
将电压降至 48V 时的一个问题是如何为终端负载(无论是非稳压负载还是稳压负载)提供所需的电力。另一个方面是如何管理能量回收制动系统的发电。在这个环节,双向转换解决方案非常重要,以便将能量回收制动系统发出的 48V 电回馈到电路和电池中。
这一点也适用于其他高级子系统,如具有能量回收功能的主动悬挂和主动转向系统。它们可能需要 48V 电压,也可能将 48V 电压反馈回电池。
例如,Vicor 的 BCMTM 母线转换器本身具有双向转换功能。它们可以在无需控制步骤的情况下完成升压或降压,自动从降压切换到升压,或从升压切换到降压。这些转换器可以感知想要的电流方向并做出反应。
Vicor 的 BCM 是高密度、高效的固定比率(非稳压)隔离 DC-DC 转换器模块,采用 ChiPTM 或 VIA 封装。这种设计简化了冷却,同时提供 PMBus® 控制、EMI 滤波和瞬态保护功能。
它们的输入电压为从 800V 到 48V,支持各种 K 因子,以支持包括汽车在内的多种应用。利用 Vicor 公司的正弦振幅转换器(SAC)拓扑,高压 BCM ChiP 能够实现 98% 的峰值效率,功率密度高达 147,000W/l3。这些 BCM 可以轻松并联成高功率阵列,且输出可以串联以实现更高的输出电压。BCM 本身具有双向转换功能,使设计人员能够减少负载所需的大容量电容。
因此,系统如何在车内完成降压、升压和切换非常重要,特别是当考虑家庭到车辆到家庭、车辆到电网到车辆等先进应用时尤其如此。汽车的电力电子设备必须继续发展,以支持这些需求和其他新兴的跨平台功能。
另一个例子是 NBMTM 系列固定比率(非稳压)、非隔离双向 DC-DC 转换器。这些模块提供了一个完整的 DC-DC 解决方案,且不需要外部输入滤波器或大容量电容。NBM2317 具备内置热插拔功能和浪涌电流限制,且其低输出阻抗可支持快速瞬态响应。NBM 系列转换器采用通孔转换器封装(ChiP)和表面贴装(SM-ChiP)封装。
线束的重量是向 48V 汽车过渡的一个重要驱动因素,也是向 48V 子系统和电机过渡的众多技术优势之一。电压越高,电机越强大、越节能,并且可以帮助缩减主电源线的尺寸。这样还可以大幅度节约成本,因为车辆线束的电线长度可能长达数百英尺。而且,更细、更轻的线束也更容易集成到车辆及其子系统中。
除了减轻主配电网络和线束的重量外,它还可以改善热管理,因为系统的效率更高,散发的热量更少。在电动汽车中,热管理对于保持电池冷却非常重要,因为电池对温度非常敏感。此外,如果能够有效地管理温度,避免系统内部故障和失效,其他电气系统的运行寿命会更长。
如果能够通过提高效率节省 100 瓦的功率,那么对燃油车来说可以将每公里的二氧化碳排放减少 1 克,或者将电动汽车的续航里程增加多达 10 公里。
在采用 800V 馈电的区域架构中,我们可以在车头到车尾的整个网络中进行单次转换,将电压降低到 48V。而在车辆中负载所在的位置上,我们可以在本地将 48V 电压降压到 12V。您只需左前和右前两个区域,而无需使电线贯穿整个车辆。然后,您可以将负载连接到这些区域。随后,在车辆后部使用 48V 主系统进行相同的操作,并连接本地 12V 负载。这样还可以使整个汽车的设计更加灵活,可以满足未来需求,在车辆迁移到其他电压和功率水平时适应各种变化。
例如,想象一个基于 Vicor BCM、DCMTM 和 PRMTM 设备的区域架构——这些设备在一个阵列中工作(见图 2)。它们可以相互通信并共享电流,以避免出现一个设备过载而另一个设备负载不足的情况。这样就可以更轻松地扩大或缩小电源系统的规模,而无需进行大量重新设计工作。
图 2:48V 区域架构(右侧)可以缩减尺寸和重量,同时提高能效。例如,线规可以从 10 号线缩小到 4 号线,进而大大减轻重量,简化设计。通过将 Vicor DC-DC 电源转换器分散到不同区域,还可以大幅度减少散热,减轻冷却系统的负载。最终,与集中式架构(左侧)相比,功率损耗可以减少 60%。
这种方法也适用于系统中仍有一个小型 12V 电池以满足功能安全要求的车辆——确保车辆的智能部分正常运行以保证安全状态。
因此,通过这三种设备,系统可以将高压 800V 电池的电压转换为 48V,而且可以进一步降压到稳压或非稳压的 12V 电压。该技术的优势之一是零电压开关,瞬态电流可达到每秒数百万安培。
由于开关速度非常快,系统可以从高压电池快速为负载供电,就像它们带有额外的低压电池一样。制造商可以将节约下来的空间和重量用于其它目的。
电气化将使原始设备制造商能够将其车辆过渡到 48V 的配电网络,利用 Vicor 的高功率密度 DC-DC 转换器模块等技术创建 48V 系统。区域架构可实现面向未来的设计,帮助根据当前和未来的功率需求进行相应的扩展或缩减。
本文最初由 Electronic Design 发布。
现任 Vicor 公司汽车客户项目总监。他在汽车行业拥有超过 33 年的丰富经验,涉及 OEM 厂商和一级供应商的制造、设计工程和产品线管理。Greg 丰富的汽车产业经验包括制造、产品开发和业务开发等。Greg 先后毕业于密歇根大学和凯特林大学,分别获航空航天工程学士学位和制造管理硕士学位。
Greg Green,汽车客户项目总监
汽车主动悬挂系统
48V 电源系统可减少损耗并缩小电源设计。Vicor 使 12V 至 48V 的过渡变得更容易,获得 竞争优势
电源模块加速汽车从 800V 到 48V SELV 的转变之路
Vicor BCM6135 为主动悬挂系统解决了历史性的电源设计问题。双向并快速瞬变的 DC-DC 转换器对全新的设计至关重要
用于电动汽车供电网络(PDN)的高压母线转换器 48V 电源模块
48V 架构可减少损耗,有助于实现更小、更轻的电源系统。Vicor DC-DC 转换器超越分立式设计,优化电源系统
Vicor 在 2025 年汽车创新日活动展示了高压至安全特低电压(SELV)转换
将高压转换至 SELV 时,软开关拓扑结构和更高频的开关技术可减轻封装重量并减小尺寸。了解有关 Vicor 电源模块的更多信息