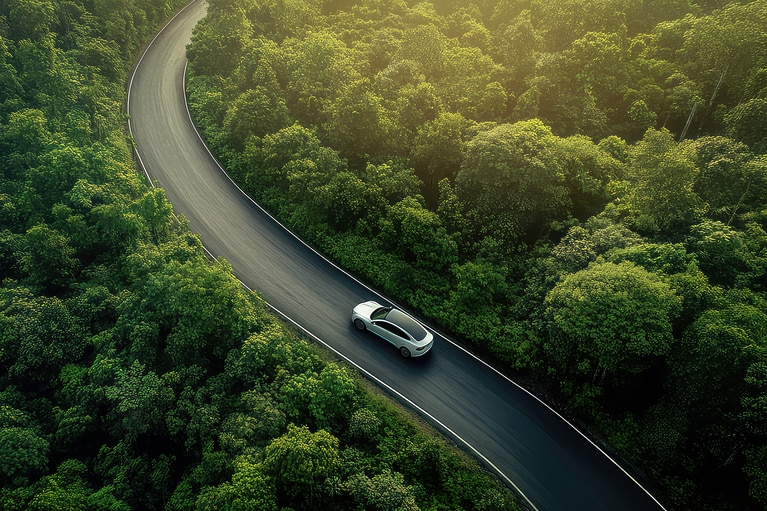
Active suspension systems in electric vehicles
48V power systems reduce losses and downsize power designs. Vicor is making the transition from 12V to 48V easier, delivering a competitive advantage
The electrification of automobiles is one of the toughest power challenges of our time. At the heart of these increasingly complex electrical systems is the 800V battery and the power conversion challenges it presents. Learn how the Vicor BCM6135 is enabling design engineers to change their approach and enabling new design opportunities.
By Patrick Wadden, Global Vice President Vicor Automotive Business Unit
The electrification of automobiles is one of the toughest power challenges of our time. At the heart of these increasingly complex electrical systems is the 800V battery and the power conversion challenges it presents. In parallel, OEMs are moving from 12V distribution network to 48V bus to capitalize on the greater efficiency that results from lower current, more power and a lighter wire harness /cabling.
So, there are multiple moving parts and the path to the perfect power delivery network (PDN) is laden with trade-offs.
For example there is a robust ecosystem of 12V loads that have been commoditized for automobiles over the decades that are not compatible with 48V. But the benefits of moving to 48V are undeniable. For example, the 12V wiring harness, one of the heaviest subsystems in today’s vehicles, can be reduced dramatically moving to 48V. It is comprised of thousands of copper wires totaling over a mile in length and weighing as much as 150 lbs (68kg). Distributing power at 48V means moving to 10AWG wiring that is less expensive and up to 85% lighter than a conventional 12V harness. This reduces size, weight, costs and design complexities. It’s an indisputable win with no significant downside.
Driving the move to 48V are power- hungry loads, such as active suspension, which has a storied history of overwhelming power engineers. 12V has never been enough to adequately power active suspension, nor many other sizable loads found in today’s vehicles. 48V combined with high-density DC-DC power modules will change the way power engineers view this one-time albatross. 48V is making it easier to power heated windscreen, power-assisted steering and braking, plus a host of pumps, fans and actuators. Together 48V and power modules will help power engineers innovate more than ever.
Converting from 800V to the SELV— or 48V nominal and below — can be complex. The architecture needs to operate at high efficiency and ensure safe operation with adequate cooling. Rapid transient response times are another important feature for many subsystems, delivering the ability to adapt to rapid changes in load while maintaining stability. This helps to ensure safe operation of loads like braking and steering where any delay can become a serious safety risk.
Conventional DC-DC converters can deliver power without the need for an intermediate battery, but the trade-off is that they are bulky and lack the fast response time required to meet the power draw by the wide variety of subsystems that require redundancy.
The high-density power module is an alternative to a traditional DC-DC converter that is having a big impact in EV power system design today. Its planar design, specialized magnetics and advanced packaging supports high efficiency, rapid response time and a very small footprint. The Vicor BCM® bus converter technology delivers low path impedance and fast response time, transforming the high voltage battery into something that can simulate a 48V or 12V battery, thus eliminating the need for intermediate energy storage. BCMs provide 98% peak efficiency and are capable of delivering up to 65A (over 3000W) of power continuously. These characteristics can support a broad spectrum of high-power PDNs in a vehicle.
Figure 1: The Vicor BCM bus converter technology delivers low path impedance and fast response time, transforming the high voltage battery into a “virtual low voltage battery” that can simulate a 48V or 12V battery, thus eliminating the need for intermediate energy storage. BCMs provide 98% peak efficiency and are capable of delivering up to 65A (over 3000W) of power continuously. These characteristics can support a broad spectrum of high-power PDNs in a vehicle.
Unlike a conventional converter, which regulates the input voltage range to a specific output voltage, a BCM converter is a fixed-ratio converter where the output voltage is a fixed fraction of the input voltage, known as the ‘K factor’. Operation is in three stages: primary-side switching converts DC input into a sinusoid, an ideal transformer stage scales the voltage by the ratio of the turns between the primary and secondary side, and secondary-side switching converts the sinusoid into a DC output.
The BCM family converts from 800V to 48V inputs with various K factors to suit a wide range of applications and markets. Based on a proprietary Sine Amplitude Converter (SAC™) topology, high-voltage BCMs can reach peak efficiencies up to 98% and achieve power densities up to 2,400W/in3. These flexible modules can be easily paralleled into high-power arrays and outputs can be put in series to achieve a higher output voltage. Additionally, BCMs are inherently bidirectional, enabling even more opportunity to innovate subsystems throughout the vehicle. BCMs also enable designers to reduce the amount of bulk capacitance needed at the load by effectively ‘reflecting’ the capacitance across the module based on the specified K factor.
Additionally, zero-current switching (ZCS) and zero-voltage switching (ZVS) topologies minimize losses. The ability to perform either a step-down conversion from high voltage to low, or step-up from low to high enables the BCM to symmetrically convert power with the same efficiency and quantity in either direction. This makes the approach well suited for applications in automotive where there is rapid charging and discharging from a vehicle power load, such as active suspension.
ZCS/ZVS switching also enables BCM converters to operate at higher frequencies than conventional converters, providing a fast response to changes in load currents and a low impedance path from input to output. Transient response times of eight million amps per second can be achieved compared with the 250A per second times when using conventional techniques.
This fast response, combined with fixed- ratio conversion, bidirectional operation and a low impedance path, enables a BCM to serve as a virtual battery, while offering reduced cable weight using lighter 10 AWG wiring. This is important because power still needs to be distributed across a vehicle’s subsystem to a mix of 48V and 12V loads. The BCM is an essential element to optimizing zonal architecture that extends 48V distribution around the vehicle before converting to 12V loads.
Figure 2: The BCM6135 is a fixed-ratio converter supporting 800V to 48V conversion. The family of BCMs are inherently bidirectional, enabling even more opportunity to innovate a variety of subsystems throughout the vehicle. With the BCM designers can reduce the amount of bulk capacitance needed at the load by effectively ‘reflecting’ the capacitance across the module based on the specified K factor. BCMs are high-density, high-performance automotive-grade converters used in today’s most innovative active suspension systems.
Figure 3: The BCM is a fixed-ratio converter supporting 800V to 48V conversion with various K factors to suit a wide range of applications and markets. Based on a proprietary Sine Amplitude Converter (SAC™) topology, high-voltage BCMs can reach peak efficiencies up to 98% and achieve power densities up to 2,400W/in3. These flexible modules can be easily paralleled into high-power arrays and outputs can be put in series to achieve a higher output voltage.
The BCM6135 has been instrumental in optimizing a historically problematic PDN. Active suspension has been a notoriously heavy, power-intensive system that is costly to design. It has plagued power designers for decades.
However, with the combination of larger primary batteries, a 48V bus and miniature DC-DC power modules, active suspension systems can be optimized like never before.
Today Hongfa, an automotive tier-one supplier, is working with Vicor to develop 800V to 48V DC-DC converters to build the ultimate active suspension system. The PDN capitalizes on 48V coupled with Vicor power modules to reduce overall size and weight. Further, it takes advantage of the BCM6135 power density to achieve a system box volume under 1.8l, and it leverages the BCM’s bidirectional power capacity to support regenerative power loads. This power design is the smallest active suspension system today — nearly half the size of the nearest competitor.
One of the greatest benefits of linking active suspension directly to the battery is energy recuperation. Similar to how a spring can absorb and expend energy, active suspension can absorb energy that be stored in the battery. While this can technically be done via a DC-DC converter, few manufacturers are able to design a system with a fast enough transient response, high slew rate, and power efficiency to manage bidirectional power flow between a device and its power source…until now.
The BCM6135 high slew rate (eight million amps per second) enables the fastest bidirectional power transfer for energy recuperation for active suspension systems. Using power modules from Vicor, Hongfa has designed the most advanced solution for powering active suspension. Not only are the Vicor DC-DC converters capable of matching the power and transient requirements to optimize energy recuperation, they also offer the highest power density in the industry enabling OEMs to reduce the overall system footprint.
Figure 4: BCM6135 enables active suspension power system size to be reduced by half. Active suspension has been a notoriously heavy, power-intensive system that is costly to design. It has plagued power designers for decades. Today Hongfa, an automotive tier-one supplier, is working with Vicor to develop 800V to 48V DC-DC converters to build the ultimate active suspension system. The system capitalizes on 48V coupled with Vicor power modules to reduce overall size and weight.
The Vicor BCM power modules embody the characteristics power engineers are seeking to solve complicated power problems. The BCM6135 is light-weight, power-dense, bidirectional and extremely fast— features needed to solve this decades-old, active suspension power problem. And this is just the beginning.
Vicor power modules enable new levels of scalability and flexibility, high efficiency and passive cooling. Power modules help reduce component count and simplify automotive power engineers’ most complex problems. The BCM6135, a compact DC-DC converter module, is the perfect a problem-solving product for today’s engineers trying to find better solutions in the rapidly-changing world of automotive electrification.
This article was originally published by Power Electronics Europe.
Patrick Wadden joined Vicor in 2018 to head up the automotive Business Unit and to drive a new end market segment for Vicor. His experience in the semiconductor industry was spread across automotive, industrial, consumer and aerospace industries with a concentration in power electronics. Patrick previously held leadership roles in sales, marketing, product line and business unit management at Intersil, Altera, ADI and Integrated Device Technology. Patrick holds a BSBA in Management at Northeastern University and lives in NH with his wife and children.
Patrick Wadden, Global Vice President Vicor Automotive Business Unit
Active suspension systems in electric vehicles
48V power systems reduce losses and downsize power designs. Vicor is making the transition from 12V to 48V easier, delivering a competitive advantage
Power modules accelerate the path from 800V to 48V SELV in automotive
Vicor BCM6135 solves historic power design problems for active suspension. Bidirectional and fast-transient DC-DC converters are essential to new design
Vicor presented converting high voltage to SELV at AID 2025
Soft switching topology and higher switching frequencies reduce package weight and size when converting HV to SELV. Learn more about Vicor power modules
BEV advancements are driving sales, but vehicle safety and reliability will ensure long-term viability
Vicor BCMs and DCMs enable easy paralleling that reduces size in the DC-DC converter, and their high efficiency and density increase performance