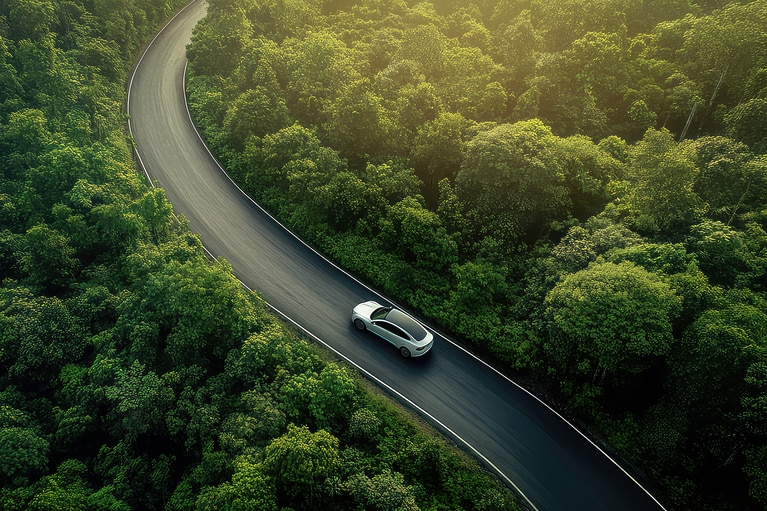
Active suspension systems in electric vehicles
48V power systems reduce losses and downsize power designs. Vicor is making the transition from 12V to 48V easier, delivering a competitive advantage
The evolution of vehicle electrification is increasing the power required to operate EVs and how designers source power for various in-vehicle systems.
By Greg Green, Director of Automotive Customer Programs
The evolution of vehicle electrification is driving changes in today’s automobile electrical design architecture. It is both increasing the power required to operate the vehicle and influencing how designers source power for various in-vehicle systems. Globally, engineers are working feverishly to solve the problem of limited range and too few charging stations. Economically, there is a lot hanging in the balance. It may be the most important power challenge engineers have ever tackled.
Battery-electric vehicle (BEV) and plug-in hybrid vehicle (PHEV) powertrains, for example, use high-voltage batteries (800V or 400V) that must also power vehicle accessories at 48V and 12V. The DC-DC converters needed to step down these loads are typically large and heavy. This can be mitigated, however, by incorporating converters based on the Vicor Sine Amplitude Conversion (SAC™) power topology. The SAC offers game-changing benefits unequaled by conventional power approaches by enabling designers to reduce DC-DC converter weight by up to 50 percent and package volume as much as 60 percent.
The electrification of the automobile is replacing electricity generated onboard with grid-generated electricity, and this energy is stored in high-voltage batteries. In addition to this change, the conversion of many control systems and subsystems, such as electric steering and suspension, ADAS and infotainment systems, presents new challenges to the power system engineer. EV power demands have increased 20x over internal combustion engines (ICE). Today’s BEVs require 100kW or more, with accessories accounting for at least 4kW of that total demand. Compare to a total power requirement of 2.5 – 4.5kW for ICE. This exponential increase poses a significant obstacle for engineers.
Figure 1: EV power demands have increased 20x over internal combustion engines (ICE). Today’s BEVs require 100kW or more compared to 2.5 – 4.5kW for ICE.
The other major change facing engineers is that power does not come from a continuously operating 12V alternator, which harvests power from the ICE. Instead, it comes from a limited supply of 400V or 800V electricity stored in the battery. Because many accessories have been cost- and performance-optimized at 12V, there is a need to preserve a 12V power supply in the vehicle. Therefore, power system engineers need an architecture to convert high-voltage battery supplies to 48V or 12V to feed the various vehicle subsystems. The ideal systems will maximize power density in order to reduce weight and unit volume.
The key to creating power-dense DC-DC convertors lies in the use of a SAC topology. The SAC process basis is zero voltage/zero current switching that enables fixed-ratio voltage conversion.
Figure 2: The SAC process basis is zero voltage/zero current switching that enables fixed-ratio voltage conversion.
To make the convertor as small as possible, the switching is done at frequencies over 1300KHz, which allows for the use of smaller magnetics and shorter path lengths for the turns. A side benefit of SAC is that it exhibits an extremely fast transient response of over 8.6MA/s.
Figure 3: The Vicor SAC topology is capable of extremely fast transient response. Here, bench testing shows a 0 – 80A load step with a slew rate of 8.6MA/s, or zero to full load in less than 10µs, which is significantly faster than a battery. An 80 – 0A load step has an even faster slew rate of 17.6MA/s.
SAC DC-DC converters have been used in high-performance computing for decades providing power density levels of more than 15kW/kg and 85kW/L. This same technology is now indispensable for automotive electrification.
Figure 4: Vicor power modules are small and power dense and are flexible enough to design architectures for charging, conversion and bridging.
The use of SAC-based devices can reduce the size of power network components and allow the power engineer to optimize the power delivery network in a number of ways. Battery-voltage power is easily converted to 48V and stepped down to 12V at the point-of-load from the 48V network. Conversion from the primary battery (400/800V) to 48V can be achieved easily using a Vicor high-voltage BCM® bus converter. Weighing only 58g and with a volume of just 0.016L, the BCM can provide 2.5kW of 48V power. The 48V power can be regulated using a high-efficiency ZVS PRM™ regulator, which weighs only 40g and is 0.01L in volume.
Regulated 48V power can be converted to 12V using a point-of-load DCM™ DC-DC regulator; a 2kW device for this weighs 29g and is 0.01L in volume. Using a SAC topology, systems can provide 2kW of regulated 12V power with only 136g of conversion devices, which reduces system weight up to 65 percent and saves up to 50 percent on DC-DC converter packaging space.
Figure 5 shows the ways that these weight and space savings can be realized in an application. This case looks at the 400V to 12V DC-DC converters in three of today’s most popular BEVs.
Figure 5: Comparing converters for some of today’s most popular BEVs offers a glimpse into the weight and space requirements that each requires.
These systems represent the best currently available, but their power density levels are quite low due to the use of standard designs based on the best available discrete component sets. These can be improved significantly through the use of the SAC topology and Vicor power modules.
In order to deliver 4kW of regulated 12V power from a 400V battery source, the system will need to use a BCM® to provide isolation and a 48V feed, and a DCM™ to convert down to 12V power. An array of two BCM6135 and two DCM3735 devices can be used to provide the necessary 4kW of power. This chipset weighs just 266g, yields 15kW/kg and takes up just 0.046L, which yields 87kW/L. To provide the full function in the vehicle, some additional circuitry is necessary, including HV connectors, LV connectors, cooling plate, housing, PCB with additional circuits (reverse polarity, pre-charge, EMI filters) and an isolator and connector for CAN communications.
With the added system components, the 4kW DC-DC converter weighs in at only 1.4kg, providing a power density of 2.5kW/kg, and is just 0.76L in volume, which delivers power density of 5.22kW/L.
Figure 6: The Vicor power converter is smaller, more efficient and is six times more power-dense than other solutions.
The resulting Vicor system is six times better in volume power density and 58 percent smaller than the current best-volume-density available from a Tesla DC-DC converter. Statistically, for every kg of weight saved, a vehicle can increase range by 0.8km. Therefore, not only does the Vicor system free more package space for other components, it delivers 1.0km more range. Furthermore, the miniaturized Vicor system is half of the weight of the Ford Mustang Mach-E system while delivering 1.7 times more efficient power density.
All vehicles, whether powered by internal combustion or fully-electrified systems, are challenged to minimize vehicle weight and optimize vehicle volume. The use of SAC-based technology to miniaturize DC-DC power conversion provides a path to achieving these goals.
The evolution of vehicle electrification is increasing the power required to operate EVs and how designers source power for various in-vehicle systems.
Greg Green is the Director of Automotive Customer Programs at Vicor Corporation. He has over 33 years of experience in the automotive industry, spanning across manufacturing, design engineering and product line management with OEM’s, and Tier 1 suppliers. Greg’s auto industry experience includes manufacturing, product development, and business development. Greg holds a B.S. Degree in Aerospace Engineering from the University of Michigan, and an M.S. in Manufacturing Management from Kettering University.
Greg Green, Director of Automotive Customer Programs
Powering innovation: Accelerate vehicle electrification with the smallest, lightest power modules
Article: Redefining automotive power delivery networks
eBook: Accelerate vehicle electrification with the smallest, lightest power modules
Article: Pump the brakes when it comes to EV fast-charging stations
Automotive products: The smallest, lightest power modules
Active suspension systems in electric vehicles
48V power systems reduce losses and downsize power designs. Vicor is making the transition from 12V to 48V easier, delivering a competitive advantage
Power modules accelerate the path from 800V to 48V SELV in automotive
Vicor BCM6135 solves historic power design problems for active suspension. Bidirectional and fast-transient DC-DC converters are essential to new design
High-voltage bus converter power modules for electric vehicle 48V power delivery networks
48V architectures reduce losses and can facilitate smaller, lighter power systems. Vicor DC-DC converters optimize power systems beyond discrete designs
Vicor presented converting high voltage to SELV at AID 2025
Soft switching topology and higher switching frequencies reduce package weight and size when converting HV to SELV. Learn more about Vicor power modules