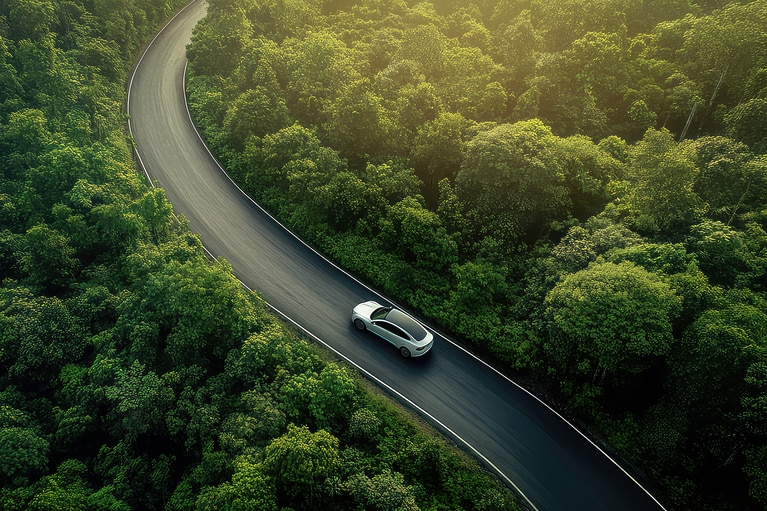
Active suspension systems in electric vehicles
48V power systems reduce losses and downsize power designs. Vicor is making the transition from 12V to 48V easier, delivering a competitive advantage
The Vicor proposal focuses on three aspects of the power delivery network architecture; charging, converting, and bridging. Redefining the architecture of a vehicle’s power delivery network saves both weight and system costs.
The growth in EV adoption is a clear and obvious trend, confirmed in several recent industry reports. While the pandemic paused car sales globally, consumers have had time to reflect on their vehicle replacement options, and it appears many are considering an EV as a viable choice. However, many potential obstacles to widespread consumer adoption exist, the most notable being range and charging time anxiety.
Still, thanks to many national and regional Government initiatives, and manufacturer special offers, EV sales are set to grow significantly in the coming years.
From the vehicle manufacturer’s perspective, there are still many technical challenges to address moving forward. The initial development of EVs sought to add EV alternatives to existing brand models for the early adopter market. However, sustained and significant growth will require technological advancements on many different fronts.
Battery design, for example, is undergoing major innovation into new chemistries and methods of construction. Although these developments are still in their infancy, there are promising results already. The deployment of a convenient and easy to access EV charging infrastructure requires significant investment too. Range and charging time remain top consumer considerations, along with price, but the key factor impacting these is the vehicle’s weight.
EVs today still maintain a 12V battery to power non-traction related functions such as windscreen wipers, seat comfort controls, and infotainment. Some manufacturers are currently replacing a 12V battery with a 48V for new models.
Any new vehicle today is equipped with a myriad of electronics-based features, a far cry from when the Hudson Motor Company introduced the concept of a standardized battery in 1918. Today, a sleek touch-controlled infotainment system typically incorporates radio, media players, a GNSS navigation system, smartphone integration, and vehicle status and systems configuration menus. In addition, vehicle occupants can stream music from their smartphone, a high-capacity SD card, or an online service. Advanced driver assistance systems (ADAS) use combinations of RADAR, LiDAR, and machine learning-based computer vision to deliver comprehensive driving aids like adaptive cruise control (ACC), blind-spot detection, and emergency braking. The advances in automotive technologies are impressive, but they all share a legacy of the past; the traditional 12V battery powers them.
For EVs equipped with a 400V or 800V battery pack, incorporating an additional battery and the associated power management electronics to power everything highlighted above would appear to incur an unnecessary bill of material cost. Figure 1 illustrates how complex the hybrid and fully EV power architectures have become compared to the internal combustion engine.
In the past, manufacturers packaged individual system functions in separate electronic control units (ECU), each powered with a 12V supply. This distributed approach to power management and conversion results in high BOM costs. Of course, BOM cost isn’t the only factor to be considered though, since the weight of a 12V primary battery and all the power components represent a significant payload. For example, the average weight of a 12V starter battery is 20kg, which, together with the excess power conversion components, can quickly become significantly increased.
Viewed another way, from the DC-DC power perspective, an electric vehicle power train introduces the need for 50kW and upwards power conversion and management compared to < 3kW for a conventional internal combustion engine vehicle. Therefore, achieving reliable and efficient power conversion in the minimum space and with the lowest weight becomes crucial. An EV power architecture needs to support the drive power train, onboard and infrastructure charging, and legacy systems.
Figure 1: A comparison of power architectures used in internal combustion engines, hybrid and fully electric vehicles.
A viable approach to solving an electric vehicle’s development challenges proposed by Vicor is to use a virtual 12V (or 24V / 48V) battery (Figure 2). Rather than rely on a separate 12V battery, why not create a virtual battery directly from the vehicle’s primary 400V or 800V battery pack? With this approach, manufacturers can save weight together with a reduction in the associated, engineering, supply chain and stocking costs.
Figure 2: Implementing an EV power architecture with virtual battery 12V and 48V sources.
By incorporating high-density HV to LV conversion modules into existing sub-systems, the Vicor approach also achieves a higher degree of integration and a reduction in BoM cost – something OEM’s wish to achieve too.
The Vicor proposal focuses on three aspects of the power delivery network architecture illustrated in Figure 2; charging, converting, and delivering.
Figure 3: Supporting legacy 12V applications through a virtual power architecture from the vehicle’s HV battery.
As automotive OEMs grapple with lowering CO2 emissions while increasing vehicle performance and functionality, electric vehicles are proving to be the best option. However, keeping electric vehicle weight to a minimum to achieve a better range is proving to be a challenge. Redefining the architecture of a vehicle’s power delivery network saves both weight and system costs.
This article was originally published by Bodo's Power Systems.
Active suspension systems in electric vehicles
48V power systems reduce losses and downsize power designs. Vicor is making the transition from 12V to 48V easier, delivering a competitive advantage
Power modules accelerate the path from 800V to 48V SELV in automotive
Vicor BCM6135 solves historic power design problems for active suspension. Bidirectional and fast-transient DC-DC converters are essential to new design
人とくるまのテクノロジー展 2025 Nagoya &ONLINESTAGE2
Vicor、ゾーンアーキテクチャの利点を最大限に発揮する48V配電ネットワークを解説
Vicor presented converting high voltage to SELV at AID 2025
Soft switching topology and higher switching frequencies reduce package weight and size when converting HV to SELV. Learn more about Vicor power modules