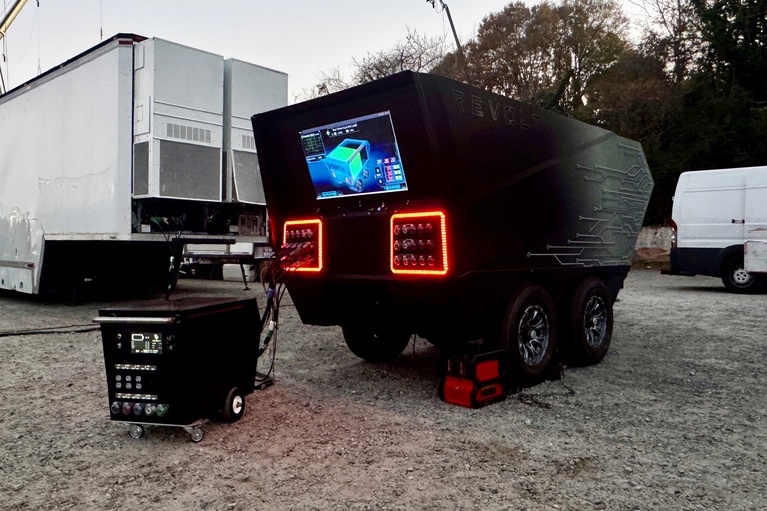
ReVolt cleans up Hollywood’s CO₂ emissions on sets with cleaner power
ReVolt charges up Hollywood’s clean energy ambitions with 48V and high density power modules. Portable renewable power offers cleaner, quieter power on sets
As the leading designer and manufacturer of high-performance power module solutions, the new facility will support a new era of growth, advancement and innovation for decades to come.
Vicor has expanded its manufacturing capacity by 2.5x with the opening of its new 90,000-square-foot, state-of-the-art converter housed in a package (ChiP™) fabrication facility in Andover, Mass. This new fab is the first of its kind, leveraging a proprietary and highly scalable approach like semiconductor wafer fabs. This vertically integrated fab utilizes patented processes enabling Vicor to set the standard for high-quality, low-cost and reliable power module manufacturing in the U.S.
Similar to semiconductor OEMs, Vicor has implemented proven and stringent fab facility processes from the ground up to ensure the highest quality. Designed with longevity in mind, the facility is equipped with industry-leading environmental controls for temperature, humidity and electrostatic discharge. The two-story building is optimized to handle immediate and future process requirements to accommodate the sophisticated ChiP manufacturing.
Vicor pioneered the proprietary panel-based manufacturing that uses a standard-size PCB, analogous to a Si wafer, in a highly automated approach to production. Multiple instances of the same high performance power module are produced simultaneously with pick-and-place capabilities for up to 420,000 components per hour on a patented substrate without compromising the accuracy or quality of the finished product. This enables Vicor to achieve 50 percent improvement in accuracy with significant increase in throughput over conventional methods. The line employs printing capabilities to achieve industry-best placement accuracy followed by advanced automated optical inspection techniques exceeding the most stringent quality standards to ensure zero-defect manufacturing.
The fab will also include specialized equipment to develop the terminal interfaces to support Vicor’s proprietary vertical power delivery solution as well as supporting ball grid array requirements that Vicor aerospace and satellite communications customers require.
The second floor has been equipped to achieve vertical integration using state-of-the-art final packaging process steps (PPS) with capacity 5x greater than the outsourced capabilities. The vertically integrated PPS operations leverage the latest advancements in automation, handling and fluid spray technology. The operation will be tied seamlessly into the Vicor central computer-integrated manufacturing architecture enabling fully automated continuous operation. The PPS operation will be maintained by a new on-site chemical process laboratory.
With a focus on environmental sustainability, the operation is designed for zero wastewater and air discharge. All waste-water will be recycled into ultra-pure deionized water that is re-used in normal operation. It is estimated this new sustainable wastewater process will save up to 20 million gallons of water each year. The new plating operation will support all the Vicor SM-ChiP™ and CM-ChiP™ package designs.
For over 40 years Vicor has been designing and manufacturing its best-in-class, high density power solutions in Andover, Mass. As the leading designer and manufacturer of high performance power module solutions, the new facility will support a new era of growth, advancement and innovation for decades to come.
This article was originally published by Microwave Journal.
ReVolt cleans up Hollywood’s CO₂ emissions on sets with cleaner power
ReVolt charges up Hollywood’s clean energy ambitions with 48V and high density power modules. Portable renewable power offers cleaner, quieter power on sets
Bidirectional bridge converters tackle 12V/48VDC-power transition
Transitioning to a 48V power distribution system is more advantageous than redesigning legacy 12V designs
Power to the stars with the largest optical telescope on Earth
Microgate has developed adaptive optics technology that to help see more clearly to deep space. Learn how Vicor power modules support their mission
DC-DC power modules help to bridge the 48V/12V transition
EVs and data centers have transitioned to a 48V architecture to enhance power performance. The new Vicor family of DC-DC converters are aiding that move